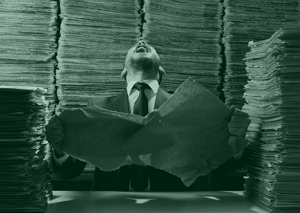
Procedure for ISO 9001 certification
What you need to know
Start your quality management ISO 9001 now
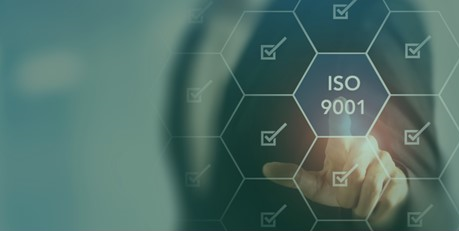
Procedure for ISO 9001 certification
1. Preliminary discussion with management
The first and most important step is the decision and full commitment of management to a quality management system. The management level must understand the need and fully support the project.2. Form a project team
We work with a project team of your choice. Involve employees from different departments who are responsible for the QM implementation. We can also act as an external quality management representative.3. Current analysis and gap analysis
An inventory of the current processes is carried out and compared with the requirements of ISO 9001 to identify gaps.4. Training and awareness raising
5. Quality policy and objectivee
Together we develop a quality policy that fits your company goals. We set measurable quality goals to meet customer requirements.6. Create documentation
We create the required lean documentation such as QM manual, process descriptions, instructions and forms.7. Implement and communicate processes
The new processes are introduced and clearly communicated to all employees through training and workshops.
8. Promote continuous improvement
We continually improve the QM system through audits, customer feedback, etc. Your employees are trained to be process thinkers.Our service: Lean, solution-oriented quality management
We offer efficient process analysis, transparent collaboration and clearly defined goals. This is how we certify your company according to ISO 9001 and ISO 14001 smoothly and with minimal effort. As doers, we implement a lean, practical quality and environmental management system. Get started today and benefit from increased efficiency, customer satisfaction and competitive advantages! We will accompany you on your way to successful certification.
Surveillance audits / recertification
As Scopewire Data GmbH, your partner for digital sustainability solutions, we know how important regular surveillance audits are for maintaining your ISO 9001 certification. After all, continuous improvement and quality assurance are at the heart of this recognized standard. Surveillance audits are a central part of the 3-year cycle of ISO 9001 certification.
They serve to check the ongoing conformity and effectiveness of your quality management system. The first surveillance audit takes place around 12 months after the initial certification, followed by the second audit another 12 months later. After the 3 years have passed, re-certification is due, during which your entire QM system is again examined in detail. Compared to the initial certification audit, surveillance audits are shorter in duration, as only parts of your QM system are checked on a random basis.
The certification body creates a detailed audit plan with the areas to be audited and time frames. This plan is sent to you in advance for preparation. For a smooth surveillance audit, all relevant QM documents such as manuals, procedural instructions and records must be up to date and available. The involvement of employees from the areas to be audited for interviews and inspections is also essential. A key checkpoint is that your company pursues a culture of continuous improvement of the QM system and that deviations are systematically processed. After the audit, you will receive a report with the results, any deviations and necessary corrective measures. At Scopewire, we are happy to support you in optimally preparing for upcoming surveillance audits. Our digital QM solutions enable seamless documentation, traceability and analysis of all relevant processes. This means you can always keep a complete overview of your certification status. Contact us for more information about our holistic offer for ISO-certified quality management.
Together we will master all challenges on the way to excellent products and services.
Frequently asked questions:
Here you will find the most frequently asked questions about ISO 9001.
The first step is to select a suitable certification body. You should pay attention to the body's experience, competence and reputation.
No, ISO 9001 certification is not a legal requirement. However, it does bring benefits such as compliance with legal requirements, competitive advantages and increased customer trust.